Stucco Cracking – What Does It Mean?
The first thing we need to understand is the difference between “cracking” and “delamination” and it is not always readily apparent. Delamination will always cause “cracking”, but “cracking” will not cause “delamination”.
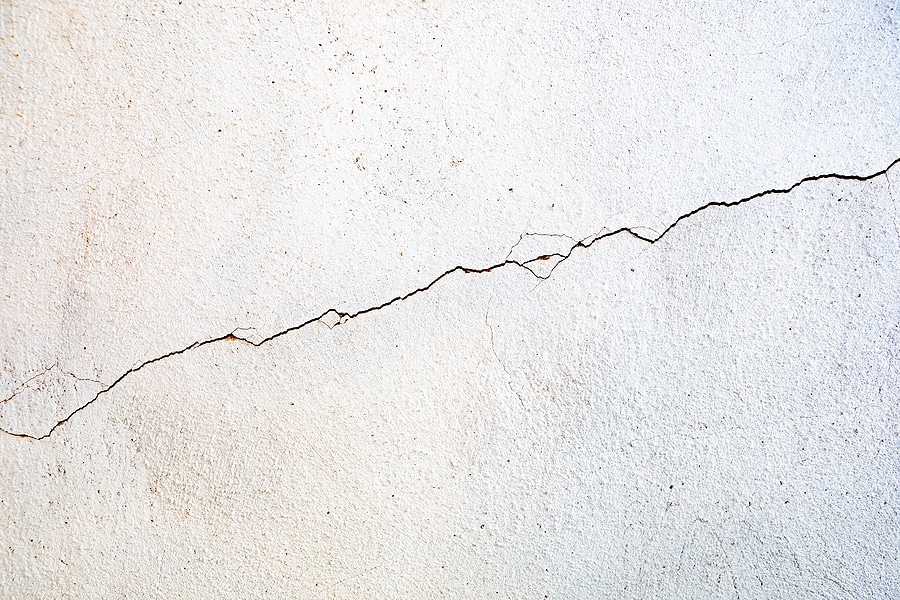
An inexperienced stucco inspector or home inspector will typically report the issue is due to “moisture intrusion” but in almost every instance, they would be wrong. Moisture doesn’t damage stucco; it’s porous and it really doesn’t care if it is wet. We get water damage to wall sheathing/studs when the moisture is trapped and doesn’t drain. That can certainly be a problem, but it doesn’t mean the stucco has failed.
Are Cracks Normal?
Stucco cracks are normal, especially in our Florida heat. Thermal loading causes stucco to expand during the day and to contract during the night. This places structural stress on the wall and stress cracks will develop in either the weakest points or the most exposed areas such as west or south-facing walls.
Problem cracks occur due to installation errors and installation errors are common in “production stucco”. Stucco wall cladding has been in use for hundreds of years and is one of the best wall cladding products available. Until the 1980s, being a plasterer was a skilled trade that required several years of apprenticeship to achieve. In short, large publicly traded, home builders killed the trade. Production builders simply won’t take the time it should take to plaster a house, nor will they pay what it should cost for a quality job.
Most people don’t understand there is no difference between plaster and stucco – they are both plasters. Plaster is typically a smooth finish installed on the interior over wood/wire lath and stucco is applied on the exterior over sheathing with a wire/plastic mesh.
What Causes Cracking?
The three biggest reasons we find problem cracking in stucco are:
- Improper embedment of the scratch coat
- Improper curing of the scratch and brown coats
- Applying the brown and finish coats to dusty surfaces
No, the biggest cause of “stucco failure” is not related to “moisture intrusion” and frankly, any inspector who reports that is misinformed and inexperienced.
Many inspectors are also quick to point out “missing control joints” which our guidelines specify to be placed every 144 square feet, but most inexperienced inspectors forget about windows, doors, wall penetrations, and corners which also serve as control joints. Back in the day when we had professional plasterers, control joints were only used at ascending floor levels, and we did not have issues with structural cracking, so I argue that placing an ugly control joint every 12 feet across the wall serves any valid purpose. I can tell you that it doesn’t stop structural cracking.
Let’s discuss the three biggest reasons we have a problem with stucco cracking:
1. Improper embedment of the scratch coat
Hard coat stucco is applied in three coats: scratch or base coat, brown or second coat, and the finish or third coat. Technically, it is a four-step process as our first step involves placing the paper and wire to which we attach the scratch coat.
Hard coat stucco should be 7/8 inches thick overall. The scratch coat is 3/8”, the brown coat is 3/8” and the finish coat is 1/8”.
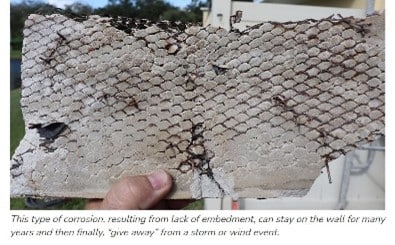
ASTM C 926 (incorporated into Florida Building Code) requires ¼” of plaster to cover both the back and front sides of the lath so that all surfaces of the lath are covered. This means all laths must be completely covered with plaster with no area exposed. When the lath is not covered, the lath will move independently of the plaster which causes stress cracking. Over time, these cracks will allow bulk water and water vapor to enter the wall and cause the lath to corrode which further allows the plaster to delaminate from the lath resulting in structural failure of the wall system.
Part of maintaining ¼” of plaster on the back side of the lath and providing a drainage plane requires the plasterer to allow a proper furr between the lath and the sheathing. All too often, we find the lath has been stapled tight to the sheathing. While the installer may “pull the wire” to allow room for embedment, this is unacceptable as not all the wire is pulled, and this creates flat spots where the plaster will not embed and we lose the drainage plane.
Wire laths should always be tied rather than fastened with mechanical fasteners. This is rarely done in production building because it takes more time/labor. Check out this YouTube video that shows lath being tied. Look closely and you will see the lath flex during troweling of the scratch coat (meaning the mud is getting behind the lath).
2. Improper curing of the scratch and brown coats
Plaster takes a long time to cure (some say years). Most of the strength comes during the first 30 days of application. Modern pre-mixes incorporate hardeners which reduces this time. Curing is a function of time and moisture. Curing slows in cooler temperatures so the process may take longer. Good stucco is dependent on the right amount of moisture and curing time.
Best practices call for a cure time of 3-5 days for a scratch coat and up to 28 days for a brown coat. Obviously, this does not happen in today’s production-building cycle. ASTM C 926 calls for a 48-hour cure time between the scratch and brown coat using a surface-mist process but it also allows for use of the double-back process which basically means the plasterer can apply the second or brown coat as soon as they think it is ready. This is basically the process being used today although there is still one very important step being missed.
The plasterer is not surface misting the scratch coat to keep the stucco hydrated
Much of our stucco is applied during hot weather in Florida and temperatures can easily be 80+ degrees Fahrenheit at 8 pm. Chances are the scratch or brown coat applied on the home has not been hydrated in hours (if at all). It is not unusual to find the plasterers do not have a water source at the property. Often, they fill buckets with water at a location down the street designated as the water source. Surface misting requires misting the walls with water with a garden hose/sprayer. Without a water source and a garden hose, the plasterer has no way to mist the stucco to keep it hydrated.
If the double-back method is being used (and it is), how would the plasterer know if the scratch coat is ready to accept the brown coat? I would accept the opinion of a truly qualified plasterer with years of experience but that is not who is doing most of the plastering today. If you don’t believe me, take a ride out to a local job site, and look around for yourself. Perhaps even more important, how would the builder know and if you pressed them for confirmation, what would they say to satisfy you? The fact is, most builders would not know.
Unfortunately, under pressure from stucco manufacturers (citing improved mix designs) and builders (looking for relief from best practices), ASTM C 926 authorized the use of the double-back coating in X1.4.2.2, citing the need to “reduce water loss” (because they know plasterers are not hydrating the stucco!). In 8.2, ASTM specifies the next coat may be applied as soon as the underlying coat has enough rigidity to resist cracking or other physical damage when the next coat is applied. I ask, “how would a plasterer know when it is proper to install the next coat?”
The modification to the ASTM C 926 Standard will only increase the buyer’s liability while reducing legal exposure to stucco manufacturers and builders. ASTM kicked the homeowner to the curb.
If you hire Property360 to conduct phase inspections of your home,
here is one method we use to check your stucco.
One way to know if the stucco is cured and ready for the next coat is to use the Mohs Hardness Test. The Mohs Hardness Scale is used as a convenient way to identify minerals. A mineral’s hardness is a measure of its relative resistance to scratching, measured by scratching the mineral against another substance of known hardness on the Mohs Hardness Scale. Remember, this is a tool and should only be used for a rule-of-thumb reference.

Scratch the surface of the plaster/stucco with a penny.
If the wall scratches the penny, the wall is cured.
If the penny scratches the wall, the wall is not cured.
Ask your builder if he checked the wall between coats and then ask, how?
3. Applying the brown or finish coat to dusty walls.
Stucco, like paint, will not adhere to dusty surfaces. Remember, I pointed out that many home building sites do not have a water source on site, and I have never, ever, witnessed a plasterer brushing or air-blasting walls prior to installing a finish coat. You should know, few, if any, painters wash walls before painting on new construction either. Why would they insist on pressure washing an existing home before repainting but completely neglect to do so on new construction? Just because it’s new, doesn’t mean it’s not dirty/dusty. Hint: The builder doesn’t want the mess and there just may not be water on site to use, so it’s just not necessary for new construction.
More delamination of stucco is caused by improper adhesion due to dirt and improper embedment than moisture, yet most home inspectors or stucco inspectors commonly cite “moisture” as the problem. Understand, if the stucco did not structurally crack or delaminate, moisture would not have intruded! Moisture intrusion damages wood sheathing and wall framing – not stucco. Unless moisture is pooling and freezing in a cold climate, it will not delaminate stucco although it can corrode lath and fasteners causing the stucco to delaminate from the lath. Again, this would not occur if the stucco was properly embedded around the lath and had sufficient drainage.
Hard coat stucco is one of the best wall cladding systems available to Florida homeowners but like any other wall cladding material, proper installation is critical to performance. Stucco should be installed using best practices and never to the minimum building code (which is what is provided by most builders). Building code does not protect you. Most stucco problems become evident as major concerns in about 3-5 years. Builders routinely shrug off initial concerns citing “normal stress cracking” and then later they blame the issue on your “failure to maintain the home”. Production builders do not rely upon you for repeat business and in fact, repeat customers are rare. For the most part, they want to sell you a home and then never hear from you again. Wall Street does not judge a national home builder on customer satisfaction; they are judged on financial performance.
Stucco Inspection Experts
Property360 provides qualified EIFS/Stucco evaluations and inspections in Jacksonville, St. Augustine, Lake City, MacClenney, Fleming Island, Lake Butler, Orlando, Palm Coast, Ormond Beach, and more. Other areas may be available upon request. Contact us today at (904) 606-1570 to request an inspection today!